Why CSOs should coach organisations toward sustainable manufacturing and product lifecycle excellence
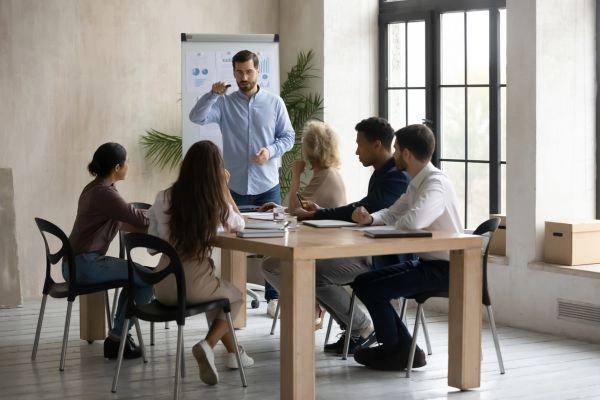
In an era where resource scarcity, regulatory pressure and consumer expectations are reshaping business fundamentals, the Chief Sustainability Officer has emerged as a critical architect of organisational transformation. Perhaps nowhere is this role more vital – or more complex – than in guiding companies toward circular economy principles that fundamentally reimagine how products are designed, manufactured and sustained throughout their lifecycles. The CSO who masters this domain doesn't simply implement sustainability initiatives; they become the strategic coach, technical guide and visionary expert who helps entire organisations rethink their relationship with materials, waste and value creation.
Understanding the circular economy imperative
The linear "take-make-dispose" model that dominated industrial manufacturing for centuries is rapidly becoming economically and environmentally unsustainable. Raw material costs are rising, waste disposal expenses are escalating and regulatory frameworks increasingly penalise organisations that fail to account for the full lifecycle impact of their products. Meanwhile, consumers and business customers are demanding products that demonstrate genuine environmental stewardship through measurable circular economy principles.
For the CSO, this transformation represents both challenge and opportunity. The challenge lies in the complexity of circular economy implementation, which requires fundamental changes to product design, manufacturing processes, supply chain relationships and customer engagement models. The opportunity lies in the substantial value creation potential of circular approaches, which can simultaneously reduce costs, enhance brand positioning, improve risk management and unlock new revenue streams.
The most effective CSOs understand that circular economy transformation cannot be imposed from above through policy mandates or compliance requirements. Instead, it must be cultivated through patient coaching, expert guidance and collaborative problem-solving that helps teams throughout the organisation discover circular solutions that align with their specific operational realities and business objectives.
The CSO as strategic coach
Successful circular economy implementation requires more than technical expertise – it demands the kind of organisational change management that transforms how people think about fundamental business processes. The CSO must serve as chief coach, helping teams across design, manufacturing, procurement and operations develop new mental models that prioritise resource efficiency and lifecycle thinking.
This coaching role begins with education but extends far beyond simple knowledge transfer. The CSO must help teams recognise circular economy opportunities within their existing work, provide frameworks for evaluating potential initiatives and support the iterative experimentation necessary to develop effective circular solutions. This requires both technical knowledge and interpersonal skills that enable productive collaboration across diverse functional areas.
Manufacturing teams, for example, often possess deep expertise in production processes but may lack familiarity with circular design principles or alternative material options. The CSO serves as a bridge, helping these teams understand how circular approaches can enhance rather than complicate their operational objectives. This might involve guiding discussions about modular product architectures that facilitate repair and refurbishment or exploring manufacturing process modifications that enable greater use of recycled inputs.
Design teams present different coaching opportunities and challenges. While many designers are enthusiastic about circular principles, they may struggle to balance aesthetic and functional requirements with lifecycle considerations. The CSO must help these teams develop design methodologies that systematically integrate circular thinking into creative processes, providing tools and frameworks that support innovation rather than constraining it.
Procurement teams require coaching that helps them evaluate suppliers and materials using circular economy criteria while maintaining cost and quality standards. This involves developing new vendor assessment frameworks, exploring innovative contracting structures that incentivise circular practices and building relationships with suppliers who can support circular economy objectives.
A systems approach to reducing virgin material usage
One of the most impactful areas where CSOs can drive circular economy transformation is in systematically reducing organisational dependence on virgin materials. This effort requires comprehensive understanding of material flows, supplier capabilities and product performance requirements that enables strategic substitution of recycled, bio-based or remanufactured inputs.
The CSO’s role as expert guide is crucial in managing the challenges of material substitution.Different materials present unique challenges in terms of quality consistency, supply reliability, regulatory compliance and performance characteristics. The CSO must help teams evaluate these trade-offs systematically, developing decision-making frameworks that balance circular economy objectives with operational requirements.
Successful virgin material reduction often begins with detailed material auditing that identifies the largest volume applications and evaluates substitution opportunities based on technical feasibility and business impact. The CSO guides this analysis, helping teams understand not just what materials are being used, but why specific material choices were made and what alternatives might be viable.
Collaboration with suppliers becomes essential in this process. The CSO must coach procurement teams in developing supplier partnerships that support circular material sourcing while ensuring quality and reliability standards. This might involve working with suppliers to develop closed-loop material recovery systems, exploring innovative recycling technologies or establishing take-back programs that create feedstock for circular manufacturing processes.
Quality assurance represents another critical area where the CSO's expertise proves invaluable. Teams often express legitimate concerns about the performance reliability of recycled or alternative materials. The CSO helps address these concerns through systematic testing protocols, pilot programs and performance monitoring systems that build confidence in circular material choices while maintaining product quality standards.
Extending product lifecycles through design innovation
Product lifecycle extension represents perhaps the most sophisticated application of circular economy principles, requiring integration of design thinking, manufacturing capability and customer engagement strategy. The CSO serves as both technical expert and strategic advisor, helping organisations develop comprehensive approaches to durability, repairability and upgradability that extend product utility while creating new value propositions.
Design for circularity requires fundamental shifts in how product development teams approach their work. Instead of optimising primarily for manufacturing cost and initial performance, circular design prioritises lifecycle value through strategies including modular architecture, standardised components, accessible repair interfaces and material selection that supports end-of-life recovery. The CSO guides these design conversations, helping teams understand how circular principles can enhance rather than compromise product appeal and functionality.
Manufacturing teams require coaching in production processes that support lifecycle extension. This might involve developing assembly methods that facilitate disassembly and component recovery, establishing quality control systems that ensure long-term durability or creating manufacturing flexibility that enables economical small-batch production of replacement components. The CSO helps these teams understand how manufacturing decisions early in the product lifecycle create opportunities or constraints for later lifecycle extension activities.
Customer engagement strategies become crucial for successful lifecycle extension and here the CSO's role as organisational coach proves especially valuable. Many companies struggle to develop business models that capture value from extended product lifecycles rather than accelerated replacement cycles. The CSO helps teams explore innovative approaches including product-as-a-service models, comprehensive maintenance programs, upgrade and refurbishment services and take-back programs that create ongoing customer relationships while extending product utility.
Building organisational circular economy capability
The most effective CSOs recognise that successful circular economy transformation requires systematic capability building that extends throughout the organisation. This involves more than training programs or policy development; it requires creating organisational systems and processes that systematically integrate circular thinking into routine business activities.
Cross-functional collaboration represents a foundational capability that the CSO must actively cultivate. Circular economy initiatives inevitably require coordination across design, manufacturing, procurement, marketing and customer service functions. The CSO serves as both facilitator and coach, helping these diverse teams develop shared vocabularies, aligned objectives and collaborative work processes that support circular economy objectives.
Measurement and tracking systems require particular attention, as circular economy benefits often manifest over longer time horizons than traditional business metrics capture. The CSO guides the development of measurement frameworks that capture both financial and environmental value creation from circular initiatives, helping teams understand and communicate the business impact of their circular economy work.
Innovation processes must be adapted to support the systematic experimentation necessary for circular economy development. The CSO coaches teams in developing rapid prototyping capabilities, pilot program methodologies and iterative improvement processes that enable effective circular solution development while managing implementation risks.
Overcoming implementation challenges
Every CSO pursuing circular economy transformation will encounter resistance rooted in legitimate operational concerns, financial constraints and organisational inertia. The most effective approach to these challenges combines technical expertise with coaching skills that help teams work through concerns collaboratively rather than dismissively.
Cost concerns represent the most common source of resistance to circular economy initiatives. Teams often focus on increased material costs or process complexity without considering lifecycle value creation or risk mitigation benefits. The CSO must guide comprehensive financial analysis that captures total cost of ownership, revenue enhancement opportunities and risk-adjusted returns from circular investments.
Technical concerns about product performance or manufacturing reliability require patient coaching that acknowledges legitimate engineering considerations while exploring creative solutions. The CSO helps teams develop systematic approaches to performance validation, pilot testing and gradual implementation that build confidence in circular approaches while maintaining product quality standards.
Supply chain complexity often creates implementation barriers, particularly for organisations with established supplier relationships and procurement processes. The CSO guides the development of supplier engagement strategies that build circular economy capability throughout the supply chain while maintaining cost and quality performance.
The strategic value of circular economy leadership
Organisations that successfully implement circular economy principles create sustainable competitive advantages that extend far beyond cost reduction or regulatory compliance. Circular approaches often unlock innovation opportunities that differentiate products in crowded markets, create customer loyalty through superior value propositions and build organisational resilience against resource scarcity and price volatility.
The CSO who masters circular economy coaching and guidance becomes invaluable to organisational success in ways that extend far beyond traditional sustainability metrics. These leaders help their organisations develop competitive capabilities in resource efficiency, innovation processes and customer engagement that create lasting value in increasingly resource-constrained markets.
Brand positioning benefits from authentic circular economy leadership often exceed the direct operational benefits of reduced material usage or extended product lifecycles. Consumers and business customers increasingly evaluate suppliers based on demonstrated circular economy commitment, creating market advantages for organisations that can credibly communicate circular practices and outcomes.
Your role as circular economy expert
The transition to circular economy principles represents one of the most significant business transformations of our time, creating unprecedented opportunities for CSOs who develop deep expertise in circular design, manufacturing and business model innovation. This expertise involves both technical knowledge and organisational coaching capabilities that enable effective change management in complex operational environments.
Your success as a circular economy champion depends not just on understanding circular principles, but on developing the coaching and guidance skills that help diverse teams throughout your organisation discover and implement circular solutions that create genuine business value. This requires patience, persistence and the kind of collaborative leadership that builds organisational capability rather than simply implementing isolated initiatives.
The circular economy transformation is inevitable – resource constraints, regulatory pressures and market expectations will eventually force all organisations to adopt circular approaches. CSOs who develop circular economy expertise now will help their organisations capture first-mover advantages while building the organisational capabilities necessary for long-term success in a resource-efficient economy.
The question isn't whether your organisation will eventually adopt circular economy principles – it's whether you will lead that transformation or react to it. The opportunity to serve as circular economy coach, guide and expert represents one of the most impactful roles available to today's sustainability professionals. The time to develop these capabilities and drive this transformation is now.