How CSOs are building sustainability capabilities in manufacturing
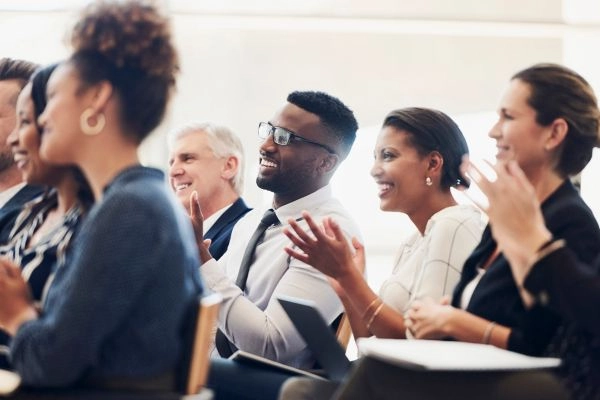
The modern Chief Sustainability Officer is increasingly taking on a role that extends far beyond traditional policy development and compliance oversight. As sustainability transforms from a peripheral concern to a core operational imperative, CSOs are becoming hands-on coaches for manufacturing teams, building internal capabilities that enable organisations to implement circular economy principles, leverage material science innovations and optimisetheir comprehensive environmental and social impact. This coaching role represents a fundamental shift in how sustainability expertise is developed and deployed within organisations, moving from centralised specialist functions to distributed capabilities embedded directly in manufacturing operations.
The evolution from advisor to coach
Traditional sustainability leadership often operated through an advisory model, where CSOs and their teams would analyze manufacturing operations, identify improvement opportunitiesand recommend changes to be implemented by operational teams. While this approach could generate valuable insights, it frequently created implementation gaps between sustainability strategy and manufacturing execution. Recommendations developed in isolation from operational realities often faced resistance, required significant adaptation or failed to achieve their intended impact.
The coaching model represents a more collaborative and effective approach. Rather than simply providing recommendations, the CSO works directly with manufacturing teams to build their understanding of sustainability principles, develop their analytical capabilities andempower them to identify and implement improvements autonomously. This approach recognises that manufacturing professionals possess deep operational knowledge that, when combined with sustainability expertise, can generate more innovative and practical solutions than either perspective could achieve independently.
The coaching relationship also creates more sustainable change within organisations. When manufacturing teams develop their own sustainability capabilities rather than relying on external guidance, they become more committed to long-term implementation and more capable of continuous improvement. They can respond more quickly to emerging opportunities and challenges while maintaining momentum even when sustainability leadership attention shifts to other priorities.
Building circular economy understanding in manufacturing
One of the most critical areas where CSO coaching proves essential is in developing manufacturing team understanding of circular economy principles and their practical application. The circular economy represents a fundamental shift from traditional linear "take-make-dispose" models to regenerative approaches that eliminate waste, extend product lifecycles and optimise resource utilisation. However, implementing these principles requires deep operational knowledge combined with systems thinking that many manufacturing professionals may not have encountered in their traditional training.
The CSO's coaching role involves helping manufacturing teams understand how circular economy principles apply to their specific operations, products and supply chains. This includes developing awareness of material flows, identifying waste streams that could become inputs for other processes and recognising opportunities for product design modifications that enable recycling, remanufacturing or extended use.
Effective coaching in this area requires translating abstract circular economy concepts into concrete operational practices. Manufacturing teams need to understand how design for disassembly affects their production processes, how material selection impacts end-of-life options and how process modifications can eliminate waste streams or enable resource recovery. The CSO must help teams develop the analytical frameworks and assessment tools needed to evaluate circular economy opportunities while maintaining focus on operational efficiency and quality requirements.
The coaching process also involves helping manufacturing teams understand the broader systems implications of circular economy implementation. Changes in one area of operations often create ripple effects throughout the value chain, requiring coordination with suppliers, customers and other stakeholders. The CSO helps manufacturing teams develop the systems thinking capabilities needed to identify and manage these interconnections effectively.
Material science innovation and selection guidance
Material science represents another critical area where CSO coaching can drive significant operational improvements. The rapid pace of innovation in sustainable materials, from bio-based polymers and recycled composites to advanced ceramics and smart materials, creates both opportunities and challenges for manufacturing teams. While these innovations offer potential for reduced environmental impact, improved performance or cost advantages, evaluating and implementing new materials requires expertise that combines technical material properties with sustainability considerations.
The CSO's coaching role involves helping manufacturing teams develop frameworks for evaluating new materials that integrate traditional performance criteria with environmental and social impact considerations. This includes understanding lifecycle impacts, supply chain sustainability, end-of-life options and regulatory implications of different material choices. Manufacturing teams need to learn how to assess materials not just for immediate performance requirements but for their broader implications across product lifecycles and value chains.
Coaching in material selection also involves helping teams understand the trade-offs inherent in sustainable material choices. Bio-based materials might offer environmental advantages but require different processing conditions or have different performance characteristics. Recycled materials might reduce resource consumption while requiring additional quality control measures or supply chain modifications. The CSO helps manufacturing teams develop the analytical capabilities needed to evaluate these trade-offs systematically and make informed decisions that align with both operational requirements and sustainability objectives.
The coaching process extends to helping teams stay current with rapidly evolving material innovations and regulatory landscapes. This includes developing networks with material suppliers, research institutions and industry associations that can provide ongoing information about emerging opportunities and requirements. Manufacturing teams learn to integrate sustainability considerations into their routine material evaluation and procurement processes rather than treating them as separate, specialised assessments.
Energy optimisation and management coaching
Energy represents one of the most immediate and measurable areas where CSO coaching can drive manufacturing improvements. While many manufacturing teams have experience with energy efficiency initiatives driven by cost considerations, comprehensive energy optimisation requires broader perspectives that include renewable energy integration, demand management, process electrification and grid interaction strategies.
The CSO's coaching role involves helping manufacturing teams understand the full spectrum of energy-related opportunities and challenges. This includes developing capabilities for energy auditing and analysis that go beyond simple efficiency measures to consider renewable energy potential, energy storage opportunities, demand response participation and process modification options that can reduce overall energy requirements.
Coaching in energy management also involves helping teams understand the broader implications of energy choices for carbon footprint reduction, regulatory compliance andstakeholder expectations. Manufacturing teams learn to evaluate energy options not just for cost and reliability but for their contributions to organisational sustainability objectives and competitive positioning.
The coaching process includes developing capabilities for ongoing energy monitoring and optimisation. Rather than conducting occasional energy assessments, manufacturing teams learn to embed energy analysis into routine operational management, identifying opportunities for continuous improvement and responding quickly to changing energy markets or regulatory requirements.
Social impact integration and community engagement
Perhaps the most challenging aspect of the CSO's coaching role involves helping manufacturing teams understand and address the social dimensions of their operations. While environmental impacts often have clear metrics and established assessment methodologies, social impacts can be more complex and context-dependent, requiring different analytical approaches and stakeholder engagement strategies.
The coaching process involves helping manufacturing teams develop awareness of their social impact across multiple dimensions, including workforce health and safety, community relations, supply chain labor practices and economic development contributions. Teams learn to identify stakeholders affected by their operations and develop appropriate engagement and impact assessment approaches.
CSO coaching in social impact also involves helping teams understand the interconnections between environmental and social considerations. Process changes that reduce environmental impact might also affect working conditions, community air quality or local economic opportunities. Teams learn to evaluate proposed changes comprehensively, considering both intended and unintended consequences across multiple impact dimensions.
The coaching role extends to helping manufacturing teams develop capabilities for ongoing stakeholder engagement and social impact monitoring. This includes building relationships with community organisations, labor representatives and other relevant stakeholders while developing systems for tracking and reporting on social performance indicators.
Developing internal sustainability champions
A critical outcome of effective CSO coaching is the development of internal sustainability champions within manufacturing teams. These individuals become advocates for sustainable practices, sources of expertise for their colleagues and catalysts for ongoing improvement initiatives. The CSO's role involves identifying potential champions, providing them with enhanced training and development opportunities and supporting their efforts to influence broader team practices.
Internal champions serve as bridges between sustainability strategy and operational implementation, helping to translate high-level objectives into practical actions while providing feedback on the feasibility and effectiveness of proposed initiatives. They also serve as early adopters for new tools, processes or approaches, helping to demonstrate their value and build broader team acceptance.
The development of internal champions creates organisational resilience and sustainability momentum that can persist even as leadership priorities shift or external pressures change. These individuals become embedded sources of sustainability expertise within manufacturing operations, capable of driving continuous improvement and responding to emerging opportunities independently.
Measuring coaching effectiveness and impact
Successful CSO coaching programs require systematic approaches to measuring effectiveness and impact. This includes developing metrics that capture both capability development and operational outcomes. Capability metrics might include the number of manufacturing team members trained in sustainability assessment techniques, the frequency of sustainability considerations in operational decision-making or the quality of sustainability-related analyses produced by manufacturing teams.
Operational outcome metrics focus on the tangible improvements resulting from enhanced sustainability capabilities. These might include reductions in waste generation, energy consumption or carbon emissions, improvements in material efficiency or recycling rates orenhancements in workplace safety or community relations indicators.
The measurement process also involves regular feedback from manufacturing teams about the relevance, effectiveness and practical applicability of coaching activities. This feedback enables continuous improvement of coaching approaches and ensures that development activities remain aligned with operational needs and priorities.
Building organisational learning systems
Effective CSO coaching extends beyond individual skill development to create organisationallearning systems that capture, share and build upon sustainability knowledge and experience. This includes developing documentation systems that preserve lessons learned from sustainability initiatives, communication channels that enable sharing of best practices across manufacturing locations and recognition programs that reward innovation and continuous improvement in sustainability performance.
The coaching role involves helping manufacturing teams develop habits of reflection and knowledge sharing that enable continuous organisational learning. Teams learn to document their experiences with sustainability initiatives, analyze successes and failures systematicallyand share insights with colleagues facing similar challenges.
These learning systems create multiplier effects that extend the impact of CSO coaching far beyond direct interactions with individual team members. Knowledge and capabilities developed in one area of manufacturing operations can be adapted and applied in other contexts, accelerating the pace of sustainability improvement across the organisation.
Future implications and organisational transformation
The CSO's role as manufacturing coach represents a significant evolution in how organisations build and deploy sustainability capabilities. By embedding sustainability expertise directly within operational teams rather than maintaining it as a separate specialist function organisations create more agile, responsive and effective approaches to sustainability management.
This coaching model also prepares organisations for increasingly complex sustainability challenges that require integrated operational responses rather than policy-level interventions. As regulatory requirements become more detailed and technical, as supply chain sustainability expectations become more sophisticated and as circular economy implementation becomes more widespread organisations with strong embedded sustainability capabilities will be better positioned to respond effectively.
The success of this coaching approach ultimately depends on the CSO's ability to balance technical expertise with effective teaching and relationship-building skills. The most successful sustainability coaches combine deep knowledge of environmental and social issues with practical understanding of manufacturing operations and strong capabilities for knowledge transfer and capability development.
The transformation of manufacturing teams into sustainability-capable operations represents one of the most promising approaches for achieving meaningful progress toward sustainable industrial systems. Through effective coaching, CSOs can help create manufacturing operations that are not just more efficient or compliant, but fundamentally more regenerative and socially beneficial, contributing to both organisational success and broader sustainability objectives.